The Scientific Research Behind Porosity: A Comprehensive Overview for Welders and Fabricators
Understanding the detailed devices behind porosity in welding is essential for welders and makers pursuing impressive workmanship. As metalworkers dive right into the depths of this sensation, they uncover a world governed by numerous elements that affect the formation of these small voids within welds. From the composition of the base materials to the intricacies of the welding process itself, a plethora of variables conspire to either aggravate or alleviate the existence of porosity. In this thorough overview, we will unwind the science behind porosity, discovering its results on weld high quality and introduction progressed methods for its control. Join us on this trip via the microcosm of welding imperfections, where accuracy fulfills understanding in the search of remarkable welds.
Comprehending Porosity in Welding
FIRST SENTENCE:
Exam of porosity in welding discloses essential insights right into the stability and quality of the weld joint. Porosity, defined by the visibility of tooth cavities or voids within the weld metal, is a typical worry in welding procedures. These spaces, if not properly attended to, can compromise the structural integrity and mechanical residential or commercial properties of the weld, leading to potential failures in the completed item.

To find and measure porosity, non-destructive testing methods such as ultrasonic screening or X-ray inspection are frequently utilized. These strategies permit the recognition of interior defects without endangering the honesty of the weld. By examining the size, form, and distribution of porosity within a weld, welders can make enlightened choices to enhance their welding processes and accomplish sounder weld joints.
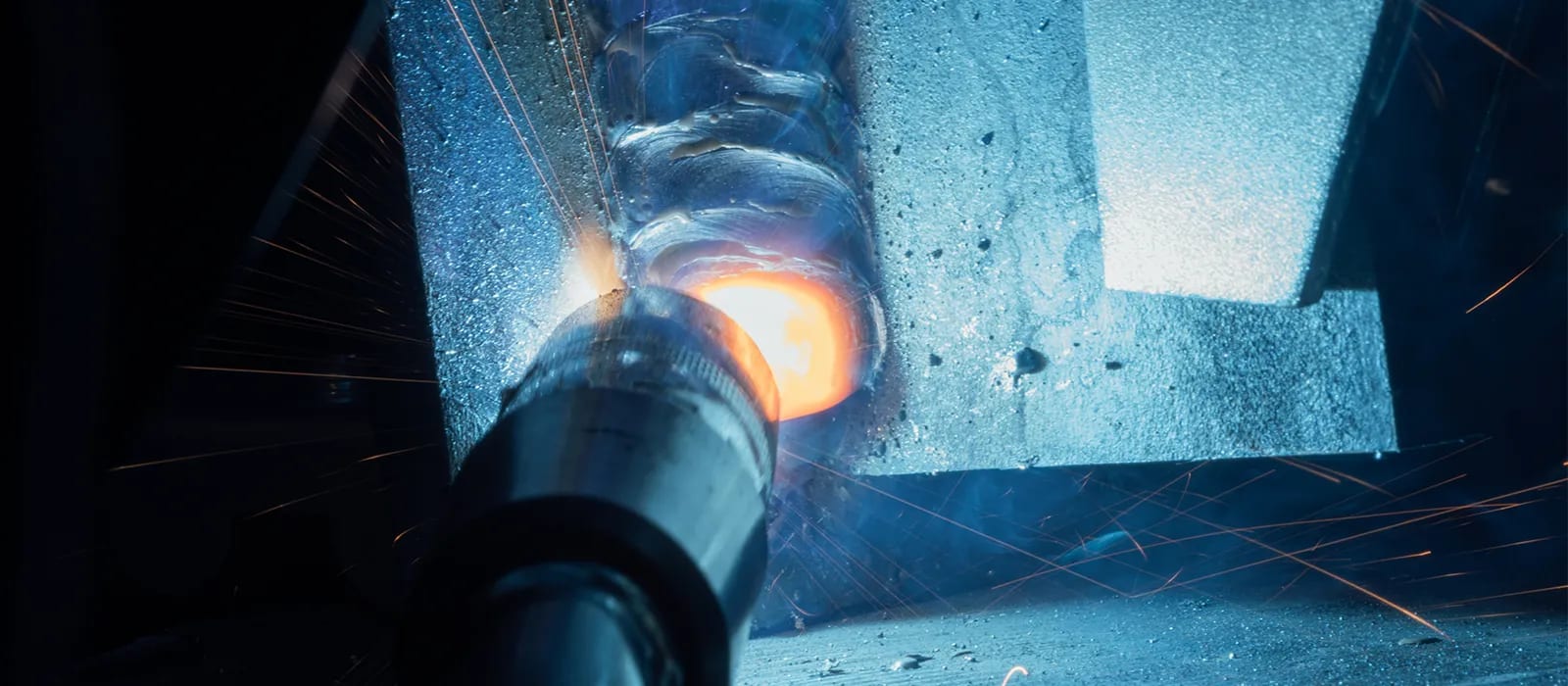
Variables Influencing Porosity Formation
The occurrence of porosity in welding is affected by a myriad of variables, varying from gas protecting performance to the complexities of welding specification settings. Welding criteria, including voltage, current, travel rate, and electrode kind, likewise effect porosity development. The welding technique employed, such as gas metal arc welding (GMAW) or protected steel arc welding (SMAW), can influence porosity formation due to variants in warm distribution and gas insurance coverage - What is Porosity.
Results of Porosity on Weld Quality
Porosity formation considerably jeopardizes the structural stability and mechanical residential or commercial properties of bonded joints. When porosity exists in a weld, it creates voids or cavities within the product, lowering the overall toughness of the joint. These gaps serve as stress and anxiety concentration points, making the weld more at risk to splitting and failing under tons. The existence of porosity likewise damages the weld's resistance to deterioration, as the entraped air or gases within deep spaces can react with the surrounding environment, bring about degradation with time. In addition, porosity can hinder the weld's ability to endure stress or effect, further jeopardizing the overall top quality and reliability of the bonded structure. In crucial applications such as aerospace, automotive, or structural buildings, where security and resilience are vital, the destructive results of porosity on weld quality can have severe effects, emphasizing the relevance of lessening porosity through appropriate welding techniques and procedures.
Methods to Reduce Porosity
To boost the high quality of welded joints and make sure architectural stability, welders and makers utilize details strategies focused on reducing the formation check it out of spaces and tooth cavities within the product during the welding process. One effective technique to lessen porosity is to make certain proper product prep work. This consists of thorough cleaning of the base metal to eliminate any type of pollutants such as oil, grease, or wetness that might add to porosity development. Additionally, utilizing the ideal welding criteria, such as the right voltage, present, and take a trip speed, is important in protecting against porosity. Maintaining a consistent arc length and angle throughout welding also helps in reducing the probability of porosity.

Utilizing the ideal welding technique, such as back-stepping or employing a weaving movement, can likewise help disperse heat uniformly and decrease the Read Full Report opportunities of porosity development. By carrying out these strategies, welders can properly reduce porosity and generate top notch welded joints.
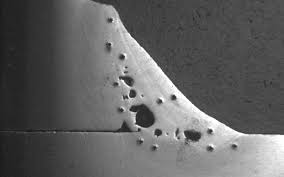
Advanced Solutions for Porosity Control
Applying sophisticated modern technologies and innovative techniques plays a critical role in achieving exceptional control over porosity in welding procedures. Additionally, employing sophisticated welding methods such as pulsed MIG welding or changed ambience welding can also aid minimize porosity concerns.
One more innovative solution entails making use of innovative welding devices. Making use of tools with integrated functions like waveform control and advanced power sources can improve weld quality and lower porosity risks. Furthermore, the application of automated welding systems with exact control over criteria can dramatically reduce porosity problems.
In addition, including sophisticated tracking and examination innovations such as real-time X-ray imaging or automated ultrasonic screening can assist in detecting porosity early in the welding process, permitting for prompt my latest blog post restorative activities. Overall, integrating these advanced remedies can significantly enhance porosity control and boost the overall top quality of welded parts.
Conclusion
Finally, recognizing the scientific research behind porosity in welding is vital for welders and makers to produce high-grade welds. By identifying the factors affecting porosity development and applying methods to reduce it, welders can improve the general weld top quality. Advanced options for porosity control can even more enhance the welding procedure and guarantee a solid and trustworthy weld. It is necessary for welders to continually educate themselves on porosity and execute best practices to achieve optimum outcomes.
Comments on “How to Identify What is Porosity in Welding and Improve Your Strategy”